The Case For Implementing A Digital Quality Management System
- October 10, 2023
- Best Practices
- Automation
Why you should take a smart approach to manufacturing quality
Reducing waste, increasing production, improving brand reputation—you probably know some of the reasons high production quality is important for your business. But do you know how costly and cumbersome addressing quality can be if you don’t take a smart approach? To help you make a business case for smarter quality management, here are five reasons to implement a Quality Management System (QMS) in your operation.
1. YOU WILL REDUCE VARIATION AND IMPROVE CONSISTENCY
By digitizing compliance documents, control plans, check-sheets and data collection with a QMS, you can simplify and automate manufacturing processes to reduce variation and improve consistency. After all, the more you can control variables in your manufacturing process, the more likely it is you will get a consistent and quality product.
A digital QMS enables you to make changes in one place and have them cascade to all relevant settings within your control plans and check-sheets. This prevents issues with changes being missed, timeliness of communication to the production team explaining the modifications, and old documentation and processes being followed because an operator missed the email.
Digitizing data and quality processes helps operators become more versatile, because they don’t have to try and be experts on the process, machine operation and required documentation and data collection all at once. Instead of making decisions based on experience and knowledge, they can use the clear data presented to them to make smarter decisions.
2. YOU WILL IMPROVE WORKFORCE RETENTION AND SATISFACTION
Taking the burden off your employees also helps them be more engaged at work. In a 2023 National Association of Manufacturers survey, more than 74% of manufacturers cited the inability to attract and retain employees as their primary challenge. Keeping your workforce happy and engaged in their work is important for retention, but not all parts of the job are fun. For instance, regulatory compliance is nobody’s favorite part of their job.
With so many government regulations and third-party certifications that have different documentation requirements, it can be complicated and frustrating to maintain compliance. With a QMS, those expectations and requirements can be integrated as part of an automated process to alleviate that workload from your workforce. The more you can automate those processes, the more you can improve the quality of work for those positions and hopefully, retain people.
Retaining your people is important because bringing in new people on the front lines of the shop floor creates risk. Will new employees record information and document data correctly as they learn new processes? Simplifying and automating the regulatory compliance part of their job minimizes the potential for human error and in turn lowers the amount of risk involved.
3. YOU WILL SAVE TIME SOLVING PROBLEMS
In addition to using data to improve consistency and optimize your manufacturing and regulatory processes, using historical data allows you to go after root cause identification at a whole new level. When problems occur, asking someone to remember how or why something happened is not always reliable. You might remember what you had for breakfast this morning, but what about a week ago or a year ago today?
With a digitized quality management system, you can stop guessing what happened and go back and discover a single point of truth based on recorded data. Without access to historical data, it could take weeks or years to determine what is causing an issue (if you do figure out), but if you can use your data to identify the root cause, you can future-proof the problem and prevent it from happening again. The result is less time resolving issues and fewer problems going forward.
4. YOU WILL SAVE MONEY ON HIDDEN COSTS
It’s easy to see some of the reasons improving quality can save money, like a reduction in waste, but there are also less obvious ways improving quality can improve your bottom line. For instance, reduction in waste doesn’t simply mean you are throwing out 100 fewer widgets. You are also producing and selling 100 more than you would have. Plus, if you don’t need rework space to fix mistakes, you could leverage that space for additional manufacturing capacity.
If poor quality products do make it out the door to your customers, customer complaints could have a negative effect on your brand’s reputation. Product recalls, lawsuits and negative public sentiment can all have lasting consequences for your long-term profitability and can be avoided by improving quality practices.
5. YOU WILL BE ABLE TO PROVE YOUR VALUE
What is the best way to get both your employees and your supervisor on board with a digital QMS? Show them how it works! Access to real-time and historical data allows you to communicate why you’re implementing certain procedures and highlight opportunities for cost reduction and capacity expansion through quality improvement. If people can see how their efforts help the company grow, they’ll be more motivated to continue creating value.
In addition to improving your own workflows and employee experience, you can talk to your customers about your production quality with definitive numbers and confidence to gain a competitive advantage.
START IMPLEMENTING A QUALITY MANAGEMENT SYSTEM
Are you interested in seeing how a QMS can work for you? Contact a member of Van Meter’s Smart Manufacturing team to discuss how you can take a smarter approach to quality management.
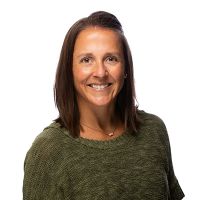
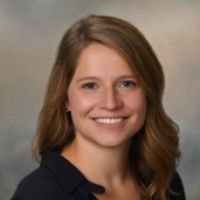
ARTICLE BY:
JACKIE LAFLEUR
EMPLOYEE-OWNER, SMART MANUFACTURING MANAGER
and
RACHEL HAHN
CIRAS, STRATEGIC ADVISOR