Arc flash best practices and tips
- January 10, 2023
- Best Practices
- Electrical
Arc flash events are among the most common source of injuries, but there are ways workers and employers can bypass them.
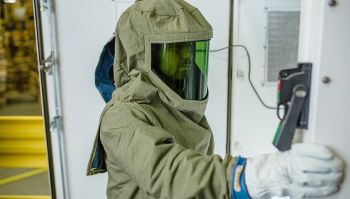
Every year, roughly 30,000 arc flash incidents occur, causing approximately 7,000 burn injuries, 2,000 hospitalizations, and 400 fatalities. Arc flashes can cause serious harm to those who work with electricity. Luckily, they’re also preventable. The more employers and employees understand about arc hazard injuries, the easier it is to avoid them and their effects.
This article breaks down the causes and impacts of arc flash events, as well as how workers and employers can bypass them.
What causes an arc flash event?
According to Occupational Safety and Health Administration (OSHA), an arc flash occurs when a flashover of electric current diverts from the intended path. It travels through the air, either to another conductor or to the ground.
Arc flash events can result from many issues, including the following:
- Accidental contact
- Condensation
- Corrosion
- Dropped tools
- Dust
- Exposure to water or other liquids
- Faulty equipment installation
- Improper preventative maintenance
- Insulation damage
- Material failure
- Obstructions
- Static electricity
The severity of an arc flash injury is based on the worker’s proximity to the hazard, the temperature, and the amount of time for the circuit to break.
Damaging effects of arc flashes
Arc flash events can cause severe damage to various body parts. The following are some of the most damaging effects:
- Eye damage/blindness
- Burns
- Hearing loss
- Lung damage
Arc flash incidents can also generate intense force and knock workers off their feet. The intensity of the fall could lead to various injuries, from broken bones to concussions.
In the resource linked above, OSHA also emphasizes the seriousness of arc flash injuries. They have the potential to be fatal.
Even if the accident isn’t fatal, it’s also common for injured employees to experience a diminished quality of life and never fully recover. Those who are injured often need extended medical care as a result of the accident.
Safety standards
Because of the grave nature of arc hazard injuries, regulatory bodies like OSHA, the National Fire Protection Association (NFPA), and the Institute of Electrical and Electronics Engineers (IEEE) have developed and implemented strict safety standards.
Here are some of the rules and regulations employers and employees must follow:
- Employees must be provided with and use appropriate personal protective (PPE) equipment
- Employers must provide a workplace free from recognized hazards, including arc flash hazards
- Employers must perform an arc flash risk assessment for all electrical equipment
- Employers must perform arc flash hazard calculations.
OSHA allows states to develop and operate safety and health programs. However, these plans must be equally or more effective than OSHA’s federal program.
Five prevention tips for workers and employers
Employers and workers both contribute to keeping the workplace safe and preventing arc hazard injuries. Here are five ways they can accomplish these goals and avoid arc flash injuries:
1. Conduct regular risk assessments
The first step to avoiding arc flash incidents is conducting regular and thorough risk assessments. An adequate evaluation includes these steps:
- Data collection: A site survey to gather information on the following:
- Utility Sources
- Fuses and Circuit Breakers
- Cables
- Motors
- Transformers
- Power systems modeling: Digital computer software compiles site-specific data into active diagrams
- Short circuit analysis: Determines the magnitude of current flowing throughout the power system at critical points
- Protective device coordination: Ensures the selection and arrangement of protective devices to limit the effects of an over-current situation to the smallest possible area
- Arc flash calculations: Based on short circuit current, protective device clearing time, and the distance from the arc
- Reporting: The inspector prepares an Arc Flash Hazard Analysis Report and full-size one-line drawings, certified by a licensed engineer
2. Clearly label all equipment
After the assessment has been conducted and the report has been completed, all equipment must be labeled based on the assessment’s results. The label should include the following statements:
- Danger or Warning header
- “Incident Energy at” indicates the appropriate working distance
- “Min. Arc Rating” is the incident energy at a working distance
- Arc Flash Boundary explains the shortest distance at which a person working may receive permanent injury
- Personal Protective Equipment (PPE) clarifies the level of protection required, ranging from 1-4
- “Limited Approach” and “Restricted Approach” fields
- “Shock Risk When Cover is Removed.”
These labels are often affixed to switchboards, panel boards, control panels, and transformers.
3. Reduce available fault current
For facilities that use non-current limiting breakers (or NCLBs), reducing the amount of available fault current can reduce the amount of incident energy released during an arc flash.
Some strategies to reduce available fault current include the following:
- Operating with an open tie during maintenance
- Employing high-resistance grounding (or HRG) systems
- Using current limiting reactors.
These strategies aren’t effective in all situations, of course. However, they can still be valuable options in some workplaces.
4. Offer adequate training
Only qualified workers should be allowed to operate equipment that could expose them to an arc flash incident. Proper training includes the following:
- Recognizing potential hazards
- Distinguishing energized and non-energized parts
- Determining exposed energized electrical conductors’ voltage
- Understanding the relationship between hazards and possible injuries
- Avoiding exposure to hazards
- Emergency procedures for assisting victims
- Performing hazard/risk analysis.
Employees should also receive regular continuing education to ensure they know the latest safety protocols.
5. Wear proper PPE
Wearing the correct personal protective equipment or PPE is another critical factor in preventing arc hazard injuries. Flame-resistant clothes and arc-resistant clothes protect the wearer from direct exposure to high temperatures.
When deciding what to wear, it’s essential to understand the difference between flame-resistant and arc-resistant clothing.
Only some flame-resistant clothing is tested for arc resistance. If an item has been tested, it will feature a specific arc rating between one and four.
Conversely, all arc-resistant clothing is also flame resistant. It protects against fire and high temperatures.
Protecting against arc hazard injuries
Arc hazard injuries can wreak havoc on an employee’s life and may even cause permanent damage.
By conducting regular risk assessments, clearly labeling equipment after evaluations, screening and training employees, and requiring proper PPE, employers can keep their team members safe, prevent arc flash incidents, and stay productive.
– DEP is a CFE Media and Technology content partner.