Life in the fast lane: comparing independent cart technology with a traditional conveyor system
- June 4, 2024
- Best Practices
- Automation
Go eight rounds comparing independent cart technology with a traditional conveyor system.
If you’ve ever been stuck in traffic because of one slow car or waited at the drive-thru because the car ahead of you needs eight Happy Meals, you know how frustrating it is when one slow-moving process delays everything else around it. The same could be said for the conveyor system on your plant floor. Why should everything move at a fixed speed to accommodate one slow process? Would you consider a faster, more flexible alternative? We compared a traditional conveyor system with independent cart technology to help you decide which makes the most sense for you.
ROUND 1: SPEED BETWEEN PROCESSES
A traditional conveyor system moves at a fixed speed, which means the whole line can only move as fast as the time it takes to perform the slowest process. It works great for rigid applications without processes that vary in time, but what happens when you have several processes that take different lengths of time to complete? If a can of paint, for example, takes five seconds to fill, three seconds to seal and two seconds to label, your cans still have to wait for five seconds at each stop along the process to accommodate for the five seconds to fill, and each can will take 15 seconds from start to finish.
With independent cart technology, you can move products at speeds up to 10 times faster than traditional systems, and as soon as a cart is done in one position, you can move it as fast as you want to its next position without waiting for other processes to complete. Now, each paint can doesn’t have to wait five seconds at each stop, and you can seal and label a can while another is filling. What used to take 15 seconds now only takes 10. When the carts are no longer containing product, they can quickly come back around to the start to be reused instead of waiting for a complete cycle to get all the way around. When you extrapolate those time savings over thousands of cans of paint, how much more could you produce in the same amount of time?
ROUND 2: PITCH OR DISTANCE BETWEEN ITEMS
In a traditional conveyor system, each flight or item on the conveyor is spaced out at equal intervals. That means each item must move the same distance at every stop along the line. Just like the speed, the pitch depends on the largest amount of space you need to perform a process. For example, if you have some 12-inch-wide boxes and some 20-inch-wide boxes, you need to have at least 20 inches between all the boxes to allow enough space for the larger ones. If each of your processes requires the same amount of space, a traditional conveyor may work efficiently.
However, you may not be fully optimizing your processes if they require different amounts of space. With independent cart technology, speed and pitch can vary at different stages of production. Because each cart is controlled individually, you don’t have to allow for maximum space between each cart. For the 12-inch boxes, you can have them 12 inches apart, and for the 20-inch boxes, you can have them farther apart. The result is optimized speed and pitch for more efficient movement regardless of size.
ROUND 3: MOVEMENT MECHANICS
More moving parts means more energy output and more opportunities for breakdown. How does the movement on a conveyor system differ from independent cart technology? While a conveyor moves along rotary driven chains, belts and gears, independent cart technology uses magnets to generate force and control all motion. Controlling motion with magnets reduces friction and makes movement more precise. Less friction means less wear on your components and more longevity for your machine. With more precise movement, you lower the chances of products colliding and causing damage to your product or machine.
Conveyors excel when higher payloads are required. Magnets are limited in the force they can supply to propel objects, so traditional conveyance methods with chains and gears are ideal for large payloads with fixed indexes and speeds.
ROUND 4: MACHINE SAFETY
Lessening the chances of collision also improves safety for your people, and independent cart technology has built-in anti-collision safeguards. Conveyor systems and independent cart technology are both relatively safe because they can utilize Rockwell Automation machine safety solutions to disable movement in the presence of operators.
Independent cart technology comes with integrated safety through Rockwell’s Kinetix® 5700 system. A traditional conveyor system can utilize the same safety system, but you have to add those machine safety components after purchase.
ROUND 5: FLEXIBILITY
The biggest advantage independent cart technology has over a traditional conveyor is the added flexibility for your machines. You can combine straight and curved sections of track to optimize your design and swap out sections to make adjustments as your production demands change. If you want to make sure your design will work before you commit to it, you can use digital twin software to test it in a virtual environment.
You can even changeover your machine to process other products or perform different functions with the push of a button. Traditionally, machine changeovers can take hours or days, but with independent cart technology, you can do it in seconds. Instead of shutting down your machine and manually swapping out parts, you can give it new instructions, and it will adjust the speed and pitch to match the new function.
On the other hand, if your machine will only be used for one product or purpose and you don’t need to changeover, a conveyor system works just as well and offers a better return on investment.
ROUND 6: PRODUCT TRACEABILITY
Some industries, like medical devices or pharmaceuticals, require everything to be highly monitored and tracked. Can you see which phase of the production process each of your items is in at any given time? Both independent cart technology and traditional conveyor systems allow you to track items through the production process, but independent cart technology allows you to trace items.
A traditional conveyor system usually requires additional sensors and machine vision components to index parts through different phases of the system. With independent cart technology, you can pinpoint where each mover is at all times and even trace it back to where it started because each mover is independent. If there is a problem you need to address, you can quickly locate where the issue occurred and take action if necessary.
ROUND 7: SIMPLICITY AND AFFORDABILITY
With so many advantages for independent cart technology, why isn’t everyone using it? Choosing which system to use often comes down to ease of implementation and cost. A traditional conveyor system is simple, easier to implement, quicker to integrate and less expensive, but you lose the flexibility, increased throughput and other benefits of independent cart technology. Independent cart technology has a higher learning curve initially, but once it is implemented properly, the payback is significant.
ROUND 8: THE FINAL VERDICT
If your machine is only going to be used for one simple purpose and you don’t need a highly flexible solution, it probably doesn’t make sense to input independent cart technology into your machine. On the other hand, if you need increased throughput, smaller machine footprint, multiple processes that take varying amounts of time and multiple products on the same machine, independent cart technology can help you achieve those goals.
If you are looking for a more flexible alternative to your existing conveyor system or technology to improve your traditional conveyor system, reach out to your Van Meter account manager or a member of our smart machines team to discuss your application or see a demo.
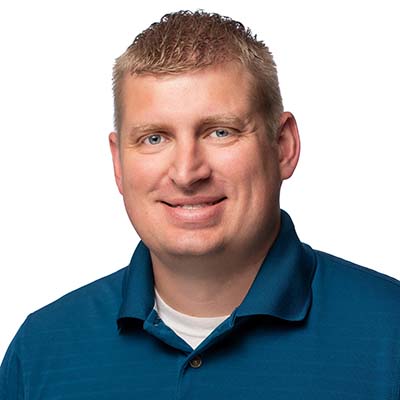
ARTICLE BY:
ZACH DOTSON
EMPLOYEE-OWNER, SMART MACHINES SOLUTION ARCHITECT