Discover the advantages of on-machine solutions in six easy steps
- October 10, 2024
- Best Practices
- Automation
Compare Centralized and De-centralized Rockwell Automation Motion Control Systems
Are you looking for ways to meet changing customer demands, reduce production time, save space on your plant floor and more? You should think outside the cabinet and discover the advantages of On-Machine™ solutions. While the hardware can be more expensive than a traditional in-cabinet solution, the total system savings, simplicity and flexibility quickly make up for it. Need more convincing? Follow these steps to discover the advantages of On-Machine solutions.
STEP 1: LEARN THE DIFFERENCE BETWEEN ON-MACHINE (DE-CENTRALIZED) VS. IN-CABINET (CENTRALIZED) SOLUTIONS
What do we mean by On-Machine vs. in-cabinet? On-Machine solutions integrate the servo drive directly onto the machinery, which allows for simple setup and quicker access. An in-cabinet solution houses components within a separate, centralized enclosure or cabinet, which can offer additional environmental protection but takes up valuable floor space and complicates design, installation and maintenance.
STEP 2: LEARN HOW MACHINE FLEXIBILITY AND SCALABILITY WILL HELP YOU ADOPT TO CHANGING DEMANDS
Housing the drives, PLCs and other components in one panel can be fine if your machine never changes, but if you never upgrade your machines, will you be able to meet the evolving demands of your customers? Adding functionality to machines typically means adding components to your panel. Will there be enough room? Can the components still function without overheating the panel?
If they will no longer fit in the existing panel, you have to purchase a larger panel then reconfigure the panel layout, determine if the internal temperature will be okay, take up additional space on your plant floor and rewire the new panel. With an On-Machine solution, your cabinet size will never change when you upgrade machines. The only components in the cabinet are the power supplies and PLC because the drives are integrated on the machine.
STEP 3: CALCULATE THE TIME, LABOR AND MATERIAL COST SAVINGS
With an On-Machine distributed servo drive, like Rockwell Automation’s ArmorKinetix® drives, devices on the machine get wired back to the drive instead of all the way back to the panel. That means you can spend less money on wire and labor when wiring your panel. In fact, an on-machine design can reduce cabling by up to 90% and lower overall system costs by an average of 30%.
“An on-machine design can reduce cabling by up to 90% and lower overall system costs by an average of 30%"
It also takes less time to design panels for the machine, as you can build more modular, standardized panels. Even as the functionality of your machine grows, your cabinet size stays the same. That means you can pre-build and pre-wire machines and put them together on your floor. When you get an order, you can wire it up with quick disconnects and send it out the door. It saves engineering time and reduces commissioning, so you’re able to meet customer demands.
STEP 4: EVALUATE THE RISKS YOU CAN AVOID
With less wiring and fewer terminations, there are fewer opportunities for human error and damaged wire. If things get mis-wired with an in-cabinet solution, it is time consuming to figure out where the error occurred because you have to trace the problem back to the panel. It’s much quicker to simply check from the device back to the On-Machine drive.
An on-machine solution also reduces your downtime risks because it’s quicker and easier to swap out the drive or drive motor if something goes wrong. You can simply swap out the drive on the machine with quick disconnects instead of getting into the panel, unwiring components and re-wiring them again.
On-Machine drives are even IP67 rated to withstand washdown and harsh environments outside the cabinet. No risk there.
STEP 5: PLAN WAYS TO USE YOUR EXTRA PLANT FLOOR SPACE
Plant floor space is valuable. Do you have a bunch of spare space to add new machines? Probably not. When you don’t have to upgrade the size of your enclosures, you can save more space on the plant floor. With an in-cabinet solution, enclosures can get really large and heavy, so you can’t put them on top or inside of the machine. Instead, the enclosures typically take up extra space next to the machine or somewhere against the wall nearby.
Moving controls and hardware closer to the point of operation with an On-Machine solution reduces control panel size by as much as 50%, allowing for reduced equipment footprint. Often, your enclosure is small enough that you can bury it within the machine instead of having a freestanding enclosure. With a smaller machine footprint, you can either add more machines (and more production!) to your plant floor or produce more with less space.
STEP 6: JUSTIFY THE HARDWARE COST
If there is a drawback to On-Machine solutions, it’s the up-front cost of the ArmorKinetix drives. But while On-Machine solutions are more costly up front, you can justify the investement with the total cost savings like:
- Simpler design
- Scalability
- Faster installation
- Reduced maintenance time
- Fewer wiring errors.
The amount of cost savings depends on the number of axes of movement on the machine. Axes of movement are the directions along which components can move, and more complex machines require additional rotational axes and multi-directional movement. Adding axes requires additional drives and motion control components and makes an in-cabinet solution much more elaborate and complicated.
If you only have three or four axes of motion, there’s not a lot of wiring required, your cabinet won’t change much in size and On-Machine solutions like ArmorKinetix might not be worth the added cost. But when you have 20 or 30 axes of motion and the potential to grow, the savings quickly add up.
THE FINAL VERDICT:
If you have a large machine with many axes of movement to control, the soft cost savings of On-Machine solutions outweigh the upfront costs.
LEARN MORE ABOUT ARMORKINETIX AND ON-MACHINE SOLUTIONS
Would On-Machine solutions like ArmorKinetix help you save time and money? If you want to discuss an application or ask questions, reach out to your Van Meter account manager, or call 1-800-247-1410 to discuss with one of our smart machines specialists.
DISCUSS AN ON-MACHINE APPLICATION
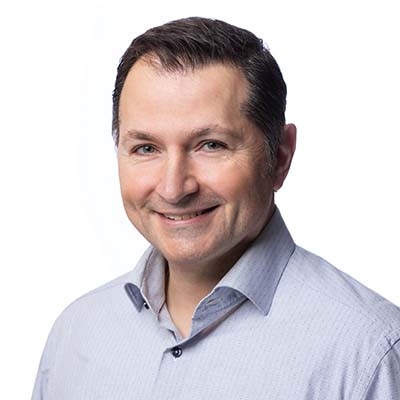
ARTICLE BY:
GEORGE ROVOLIS
EMPLOYEE-OWNER, SMART MACHINES & ROBOTICS MANAGER