Safety: An Important Part of Your Digital Transformation
- March 4, 2021
- Best Practices
- Automation
As we talk about digital transformation, there are lots of discussions about systems, KPIs, analytics, and infrastructure. But there’s another important component you don’t want to leave out: safety. It plays a big part in your success.
I recently caught up with Chris Brogli, vice president of safety business development and TUV expert at ROSS Controls. He has learned some valuable lessons in his 31 years of safety experience – from the impact of safety on your reputation to building it into your culture.
First, What Does “Safety” Mean?
Defining “safety” may seem simple on the surface: protecting people (which is absolutely vital). But its benefits go far beyond keeping workers safe.
Every 15 seconds, Brogli says someone dies from a work-related accident. During those same 15 seconds, another 160 people experience some kind of work-related accident. All it takes is one injury to have a major negative impact on your bottom line – not to mention what your employee will endure during recovery. A safety issue can even push business to your competitors.
After a workplace incident, you can expect to experience a loss of production (of course), accompanied by many other losses. You’ll likely be paying wages for work not performed as the injured employee recuperates. In the meantime, you’ll also need to pay someone new to fill that position (this person may need training to use the machine, etc.). Insurance costs will increase and, depending on what happened, you may also need to repair or replace equipment.
The Six Domains of a Culture Built on Safety
To achieve success, Brogli recommends designing your safety culture with a focus on six domains.
1. Establishing a Compelling Vision
The company’s vision should be a clear representation of what you want to achieve. It should inspire action, motivate employees to work as a team to achieve success, and communicate goals.
When everyone is guided by the same vision, it also helps reduce conflicting or competing goals. (For example: Production may want to manufacture as many parts as possible while quality likely wants to take time and make the best products they can.)
2. Valuing Trust, Respect, and Inclusion
A culture of trust, respect, and inclusion makes everyone more confident and comfortable. In these environments, you know that everyone around you has your best interests in mind. Workers at all levels are free to express themselves. They can bring up concerns about safety without being reprimanded. They can share ideas and know they’ll be taken seriously. They can remind their boss to put on PPE before coming close to a machine.
When people aren’t respected, they tend to withdraw and unplug, which can lead to unsafe situations. You can avoid this by including the right people in discussions. Workers want to be involved in conversations about safety. They have knowledge to contribute and know their processes inside and out. Make sure to bring people from different backgrounds together as well to make sure everyone understands their perspectives.
3. Selecting, developing, and engaging your board
Your board should treat safety as a top priority. This sets the tone for the rest of your organization. With a board that leads the charge and engages everyone else along the way, you can be sure they’ll support leadership as they promote a culture of safety as well. This ultimately trickles down throughout the workforce.
4. Prioritizing safety in selection and development of leaders
People naturally react based on how leadership acts. If employees don’t trust their leaders, they may not follow them.
When filling high-level positions, look for leaders who will support safety in the right ways. Will they fund necessary training and development? Will they support time spent in safety meetings?
5. Leading/rewarding a culture of safety
Whether you’re bringing in lunch, offering extra vacation time, or handing out prizes, rewarding workers who support a culture of safety motivates them to continue – and encourages others to do the same. Even a simple “thank you” can go far.
6. Establishing organizational behavior expectations
What’s considered “safe” in many cases depends on the user’s unique perspective. What one person deems safe may feel unsafe to someone else. This can cause problems in a plant environment when safety isn’t defined for everyone in the same way. What does “safe” mean to your organization?
Once safety is defined, then it’s time to document it. Does everyone know what they’re expected to do to maintain safety? Are these procedures written down and easily accessible? Are safety meetings held as planned? Are startup checklists being created and followed?
Workers can adjust their behavior accordingly when processes, expectations, and procedures are clearly documented and explained.
TRANSFORM Webinar Series
This blog is based on insights shared during the ninth webinar in Van Meter’s 11-week TRANSFORM series, which ran from Sept. 3 through Nov. 12, 2020. The series focuses on smart manufacturing and digital transformation, connecting you with industry peers who share their digital-transformation experiences and the approaches they took to get there.
Want to hear more about building your own culture of safety? Watch “The Business Case for Safety Culture and Considerations for Building a Holistic Safety Program” on demand here. Then sign up to watch other webinars in the series here!
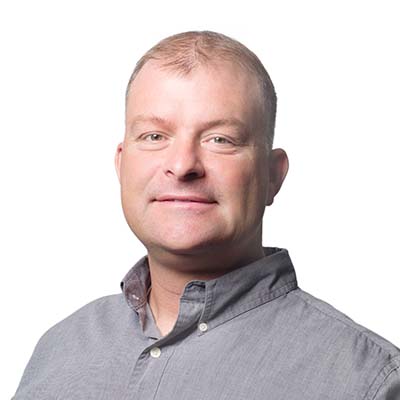
ARTICLE BY:
RANDY TURNER
EMPLOYEE-OWNER, SOLUTION CONSULTANT-SAFETY
For more information about Van Meter’s industrial controls solutions, please call 1-800-247-1410.