How To Change And Create A Safety Culture In Your Industrial Facility
- June 15, 2022
- Best Practices
- Automation
When people think about manufacturing, they may think about the three D’s: Dark, Dirty and Dangerous. Dark can be fixed with LED lighting, and Dirty can be fixed with proper hygiene, but Dangerous is the most important perception to change and requires the most effort. It starts with establishing a safety culture.
Do not establish rules. Establish a culture.
Safety should be a core value, not a priority. Your plant might have a list of rules and a sign on the wall that says, “Safety is our #1 Priority,” but if machines are not properly guarded and employees do not understand procedures, you do not have a safety culture. Rules are not enough. Instead, establish a culture where everyone takes responsibility to maintain safety protocols. While culture and expectations come from the corporate level, it is everyone’s responsibility to maintain them.
Invest in safety to get more production.
A common myth is that investing in safety requires sacrificing production, but the opposite is true. Done correctly, safety can reduce downtime by 2% to 4%, and manufacturers with safer workspaces have less than half the injury rate compared to manufacturers with less developed safety cultures. The return on investment for safety is high. If you invest in a safety culture for your people, they will stay, work, feel valued and produce more for you.
Evaluate your current situation.
If you know you need to address plant safety but do not know where to start, Van Meter offers a Safety Conformity Audit. Through the audit, our team checks all machines in the plant for proper guarding and compliance with safety standards. For example, are there cracks or gaps in the machine? Do all E-Stops have a yellow background and red mushroom push button? Each machine is then given a score. What is the overall risk of the machine? Can someone get killed or injured by it? Machines that score high (high being dangerous) will be given priority, and we can address those safety concerns first.
Let the machines do the work.
Having safety procedures that workers know and follow is an important part of a safety culture, but when it comes to machine safety, procedures should be as passive as possible. Letting the safety system do the work for you is more reliable than a person having to manually lockout/tagout—plus it saves time. Having a functional safety system allows workers to enter the machine for clearing jams or quick maintenance. It saves an average of 10 minutes of downtime compared to lockout/tagout. Lockout/Tagout is still necessary for major maintenance, but on an everyday basis, we want the machine to do it for us. If workers can rely on equipment to keep them safe, they have one less thing to worry about and can be more productive.
Measure your progress.
What is the best way to measure the success of your safety culture? How many accidents have you had in the last two years that could have been avoided? If the answer is more than one, you have work to do. You can also look at retention rates. Are people leaving in large numbers? Even without accidents, people will leave if they perceive the work environment as unsafe. Gen Z and Millennials are much less tolerant of unsafe conditions than their predecessors. With 2.7 million baby boomers retiring by 2025, establishing a culture where employees feel safe to do their jobs is more important than ever.
Van Meter can help in all areas of a safety program whether it is products, services or PPE. Contact us today to get started, and partner with us on your safety journey.
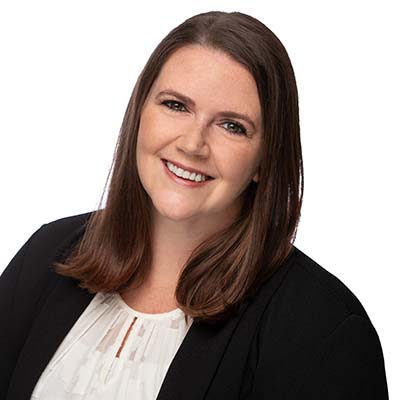
ARTICLE BY:
MICHELE SILVA
EMPLOYEE-OWNER, SOLUTION CONSULTANT - SAFETY