Improving Energy Efficiency & Sustainability with Smart Energy Management Solutions
- May 15, 2025
- Customer Success
- Automation
Go On the Job in the asphalt and petroleum industry to see real-life results regarding a strategic energy management program.
When you think of sustainability, you probably think about its positive impact on the environment. While it’s true that sustainability is healthier for our planet, it’s also good business. Did you know 98% of manufacturers surveyed in Rockwell Automation’s 2024 State of Smart Manufacturing Report have some form of sustainability and ESG (environment, social and governance) policy? In the same report, energy management was identified as the most important factor towards meeting sustainability goals.
What can manufacturers do to improve energy management? Go On the Job with Van Meter to see what an asphalt and petroleum manufacturer learned from a recent energy optimization study, and which Rockwell Automation software solutions are helping them mitigate energy consumption challenges.
CHALLENGE: IDENTIFYING OPPORTUNITIES AND SOLUTIONS FOR REDUCING ENERGY COSTS
Becoming more sustainable and reducing energy costs starts with identifying where excess energy is being utilized. The asphalt and petroleum manufacturer was seeking a comprehensive energy assessment to reduce energy costs, improve efficiency and mitigate energy consumption challenges.
Why did they focus on energy? Energy is one of the main components of their cost structure and the one they have the most control over. Reducing costs means higher profit margins.
What made energy so costly? The manufacturer was collecting data, but it wasn’t making efficient use of it. Manually documenting energy consumption and reviewing it monthly was an inefficient use of time and resources that left much of the data to become stale by the time they attempted to use it. Plus, other data sources were siloed and unavailable to support cost savings opportunities.
That’s why the manufacturer called on Van Meter’s smart manufacturing solutions for three objectives:
- Analyze energy use and costs
- Suggest metering and data collection improvements
- Assess the feasibility of implementing a cloud-based energy management solution
SOLUTION: REAL-TIME VISIBILITY INTO ENERGY CONSUMPTION
The manufacturer was not able to pinpoint opportunities to improve without first understanding their current processes and priorities. Van Meter started by providing an energy optimization study to identify gaps in the manufacturer’s energy management strategy.
The biggest issue was the manufacturer didn’t have visibility into how much energy it was using throughout the month and where their energy consumption comes from.
Van Meter’s assessment gave the manufacturer a roadmap and justification for implementing these Rockwell Automation software solutions:
FactoryTalk DataMosaix
To get a complete picture of where, how and why energy is being utilized, manufacturers need a simple way to break down data silos and optimize how industrial data is used across the enterprise. Rockwell Automation’s FactoryTalk DataMosaix is a software tool that pulls in information from several data sources and pulls it all together into a more centralized, digestible, contextualized format.
With DataMosaix, manufacturers can view information regarding temperatures, processes, engineering documents, raw materials and even the weather all in one central location. DataMosaix pulls all the information together and starts to identify relationships between those data points that the manufacturer can use to make better decisions about their processes. Plus, the data is constantly updating, so it’s always up to the minute.
FactoryTalk Energy Manager
Energy Manager is an application that uses information from DataMosaix to improve awareness of energy usage and build the foundation for a more strategic energy management program. In addition to the information it gets from DataMosaix, Energy Manager can look at specific information from different power meters. It could be electrical, water, air, gas or steam.
Instead of looking at its monthly electrical bill and wondering what caused fluctuations in cost, Energy Manager would help the manufacturer see where energy is being used and why it is using so much energy.
FactoryTalk Optix
FactoryTalk Optix is Rockwell Automation’s platform for Human Machine Interface (HMI) and data visualization. It can be deployed on-premises or in the cloud and has built-in change tracking and versioning to make scalability and collaboration easier. In this case, Optix is the foundational layer that feeds information into DataMosaix and gives the manufacturer the ability to view data from the machine level to remote access.
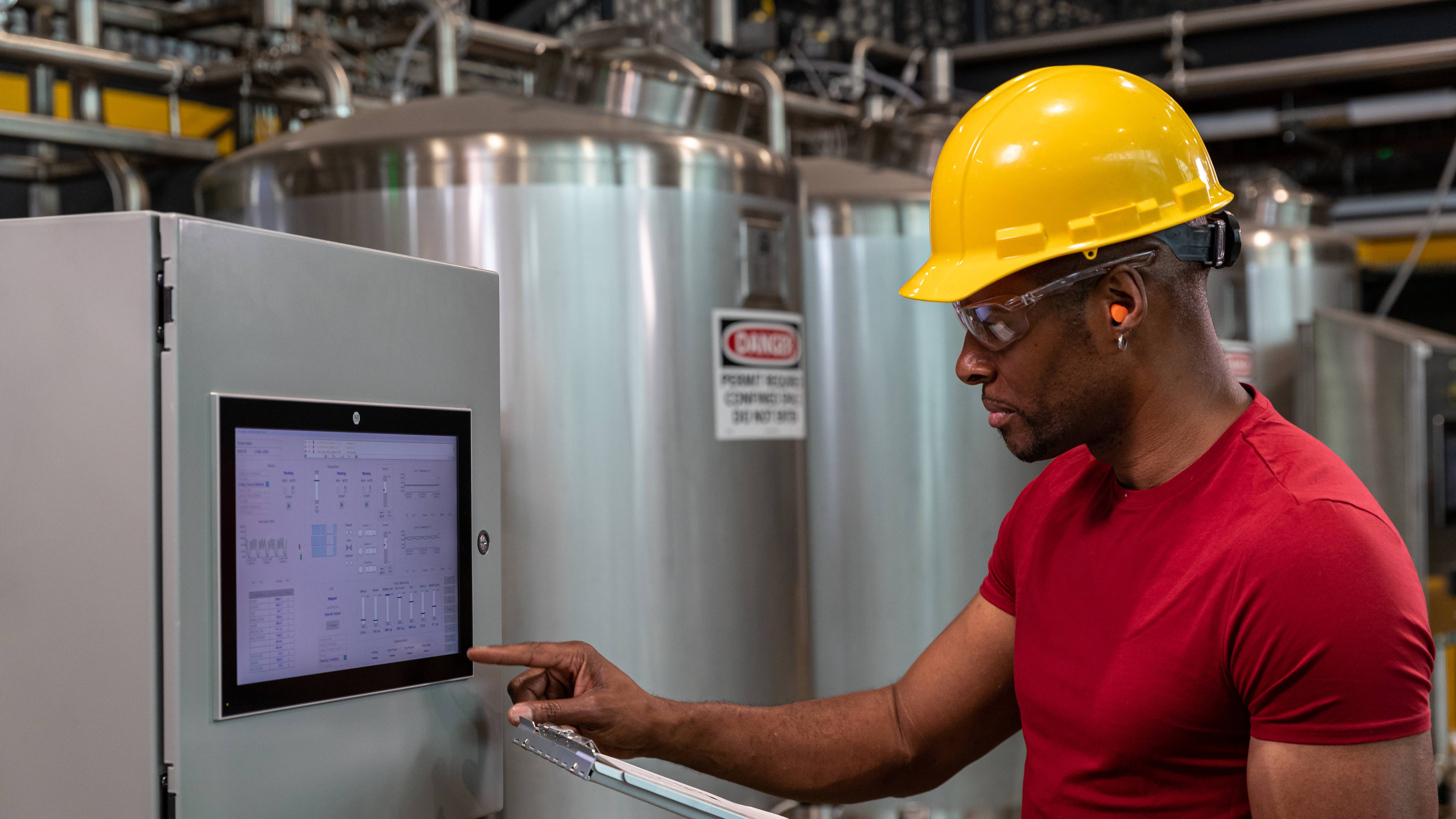
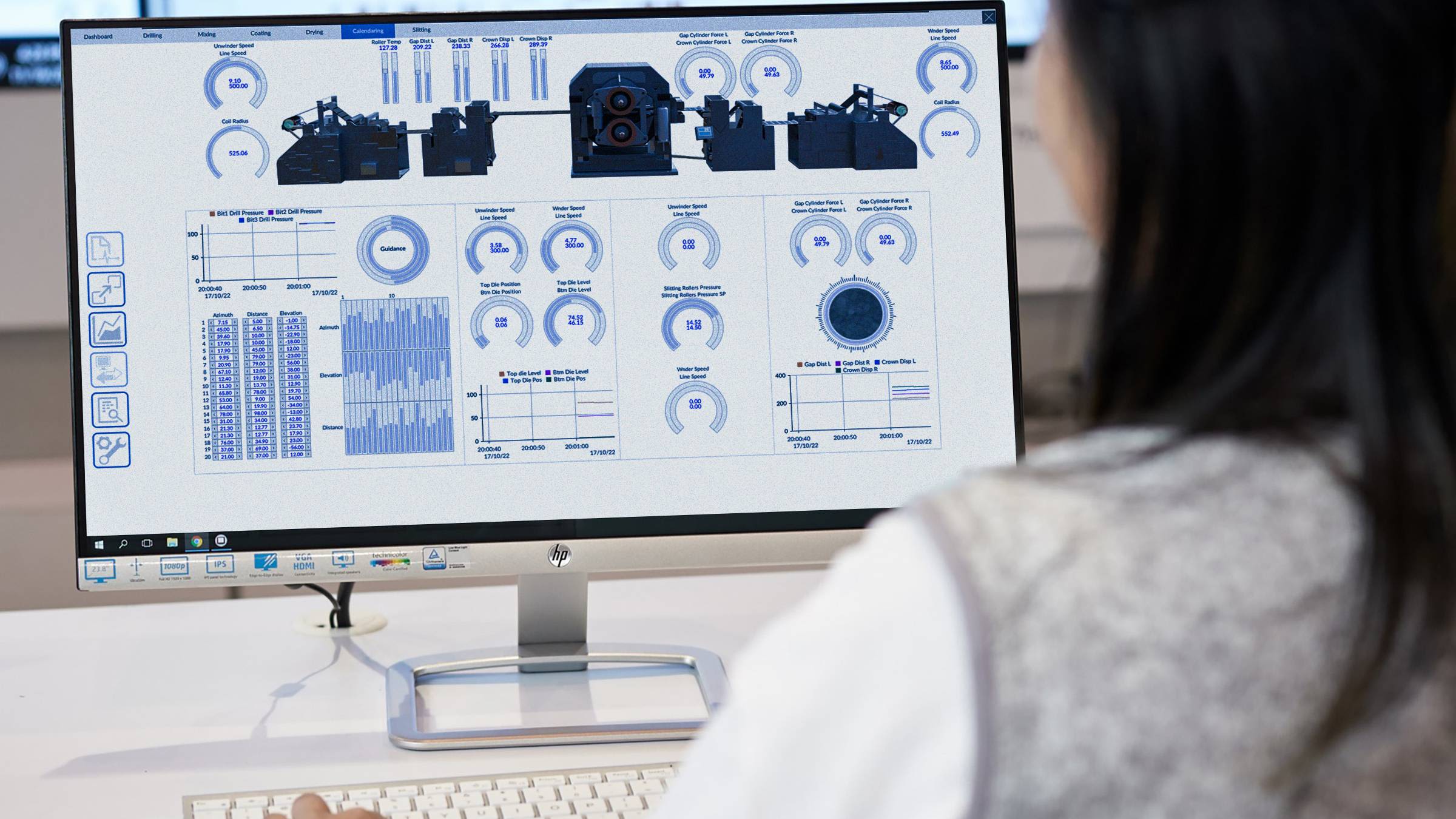
FactoryTalk Optix can be accessed at the machine level or remotely.
RESULTS: A ROADMAP FOR MORE EFFICIENT ENERGY USAGE
By providing the energy optimization study, Van Meter was able to deliver on the objectives from the start of the project:
- Analyze Energy Usage and Costs: The energy optimization study gave the manufacturer a roadmap for immediate, short-term and long-term next steps to help them improve energy efficiency. For example, separating oil and water before heating the oil for processing and insulating tanks to avoid heat loss were two cost-saving actions they could implement in the next six months.
- Suggest Metering and Data Collection Improvements: In addition to the recommended software platforms, the energy optimization study suggested some hardware improvements throughout the facility. Van Meter’s team recommended the ideal location to place meters so the manufacturer could pull more information into DataMosaix and get a clearer picture of its energy usage.
- Assess the feasibility of implementing a cloud-based energy management solution: FactoryTalk DataMosaix, Energy Manager and Optix are available via FactoryTalk Hub, Rockwell Automation’s cloud-based solution for applications. Combining the three applications into a more strategic energy management solution would help the manufacturer understand where their energy is being used and improve processes. Then it could quantify and verify that it saw an energy reduction.
In this case, Van Meter estimates the manufacturer could save almost $200,000 in annual energy expenditures with the ability to scale the solution to other locations within the total enterprise.
SCHEDULE YOUR OWN ENERGY OPTIMIZATION STUDY
Do you lack visibility into your energy usage? How much could your bottom line improve with less energy expenditure? Work with your account representative to schedule your own energy optimization study, identify opportunities for improvement and implement more efficient, sustainable energy management processes.