Less Is More: Three Ways Technology Improves Workforce Efficiency
- July 14, 2022
- Best Practices
- Automation
A workforce shortage can seem like a hockey team facing a power play while one of its own players is in the penalty box. Being outnumbered makes it harder to score, but with the right gameplan, hockey teams can still score short-handed goals. Production on a plant floor is similar. You can still score your company goals with fewer people, but if you utilize the right technology, it does not have to be more difficult. Here are three technological solutions to help you reach your goals with a smaller workforce.
1. COLLABORATIVE ROBOTS
If your operation requires people to do repetitive, physical tasks, you are risking errors, injuries and employee dissatisfaction. Using collaborative robots—or “Cobots”—mitigates that risk by automating processes that would otherwise be tedious or harmful to workers. Cobots can either work independently or safely alongside humans to make tasks more efficient, and they can be reprogrammed and redeployed for other tasks as often as needed. No matter which way they are deployed, using cobots as an extra set of hands can help you do more with fewer people.
2. AUGMENTED REALITY
You are probably more familiar with augmented reality (AR) than you realize. SnapChat filters use AR to give users puppy dog ears, beards, tattoos and more. AR is not all fun and games though. When used on a plant floor, AR can overlay diagrams and instructions onto real world objects, so workers can get directions and work simultaneously. Instead of needing another employee to help onboard new hires and waiting for them to get up to speed, AR can guide them step by step. Do existing employees need to learn a new process? AR can help them learn and perform new tasks more confidently with constant guidance.
3. REMOTE SUPPORT
Why hire one or more employees to be available around the clock when you can carry expert support around in your pocket 24/7/365? Rockwell Automation remote support is always available via phone or chat and can be bundled into an Integrated Service Agreement with repair services, e-learning and more.
Vuforia Chalk is available as a smart phone app and can assist with remote support. Think of it like John Madden drawing yellow, squiggly lines on the Telestrator during a football game. Instead of diagraming passing routes and blocking assignments, remote technical support agents can provide live video support and annotate on screen to provide instructions. Is there a specific knob you need to twist? With Vuforia Chalk, technical support can circle it on the screen to more easily walk you through the procedure.
What ways can you leverage technology to make your operations more efficient? Whether it is cobots, remote support, augmented reality or inventory and maintenance management, Van Meter has experts who can guide you through ways to reach your goals even if you are short-handed. Contact us to learn more about how any of these solutions can improve your efficiency.
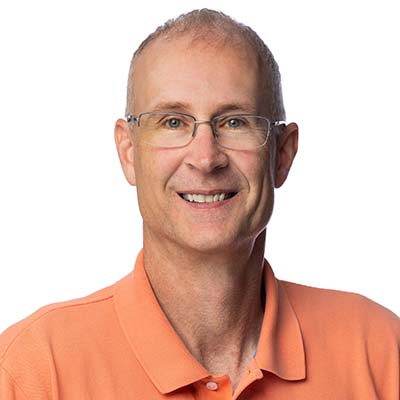
ARTICLE BY:
JEFF HAYES
EMPLOYEE-OWNER, SOLUTION CONSULTANT - LIFECYCLE SERVICES