Aiming For Autonomy in Manufacturing
- July 8, 2025
- Best Practices
What is Smart Manufacturing, and how do you start implementing it?
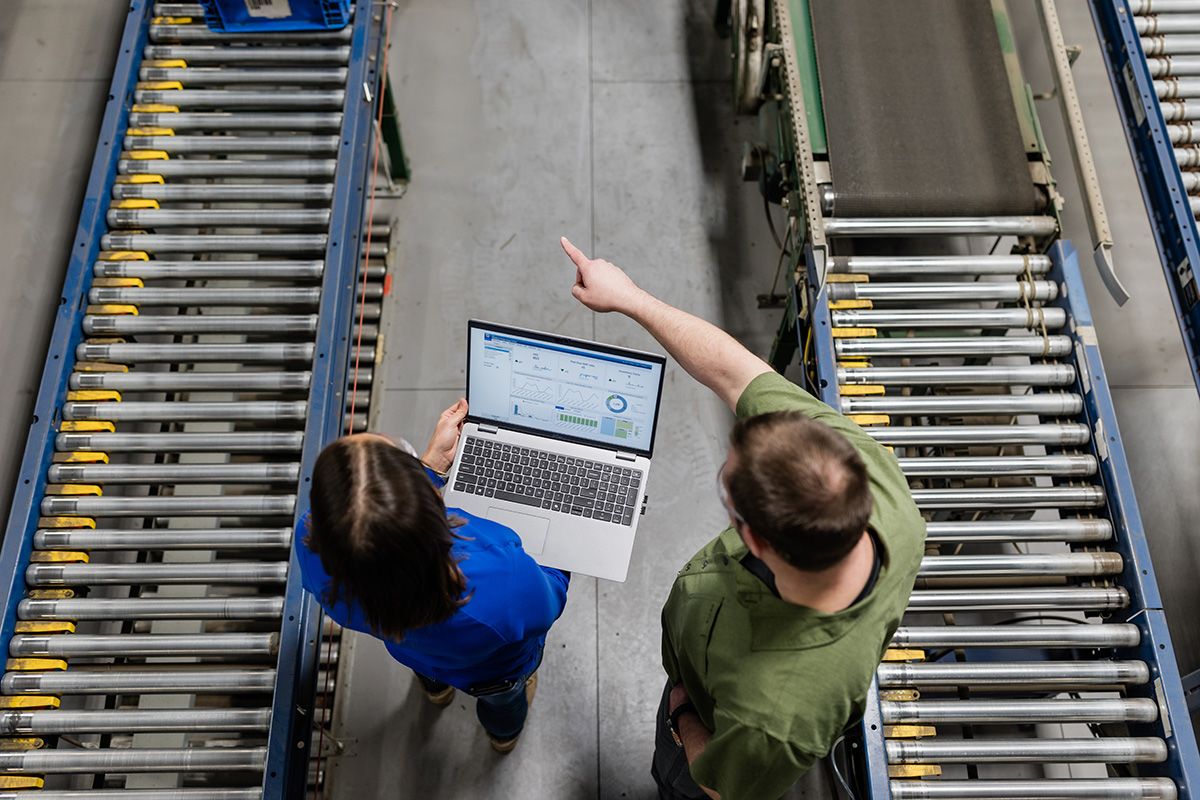
Where are you on your digital transformation journey? You’ve probably heard “the journey of a thousand miles begins with a single step,” but each step of the journey is just as important towards reaching your end goal. Manufacturers can always take steps to improve as they aim for autonomy. No matter what stage of the journey you are on, learn how to take your next steps in smart manufacturing.
WHAT MANUFACTURING CHALLENGES DOES SMART MANUFACTURING ADDRESS?
- Workforce Shortages and Skills Gaps: US manufacturing is expected to have 2.1 million unfilled jobs by 20301. Why is there a manufacturing labor shortage? A quarter of the manufacturing workforce is 55 or older.2 Manufacturers are left with skills gaps when those employees retire because it is difficult to replace years of industry knowledge and experience. In fact, manufacturers cited a lack of skilled workforce as the top reason they will struggle to outpace the competition in Rockwell Automation’s last three State of Smart Manufacturing (SoSM) Reports.
- Operational Complexity: What makes skilled labor so valuable? Industrial automation is becoming more complex as consumption becomes more personalized. In the most recent SoSM report, 83% of manufacturers said analytical thinking, communication and teamwork are the most important skills when recruiting the next generation.
- Supply Chain and Market Volatility: From supply chain delays in recent years to the current evolution of tariffs, the industrial manufacturing industry is always fluctuating. Manufacturers who lack a contingency plan and fail to adapt to changes risk falling behind the competition.
- IT/OT Integration: IT and OT teams often have different priorities and protocols when dealing with network security, which makes establishing an effective cybersecurity plan that protects the entire enterprise more difficult.
- Environmental Pressures: Sustainability is no longer an option for manufacturers. Manufacturers face increasing pressure to adopt sustainable practices from consumers, investors and regulations. In addition to reducing environmental impact sustainable practices can enhance brand reputation and even improve efficiency.
WHAT IS YOUR DIGITAL MATURITY LEVEL?
Before you can begin to address your challenges, it’s important to assess the digital maturity level of your plant. Which phase best describes your stage of the digital transformation journey?
Phase 1: Pre-Digital Plant
Pre-digital manufacturers may have automation, but those automation systems are not connected. These plants rely on manual processes and paper-based data collection and reporting, which is more tedious and error-prone than a digitized solution.
Phase 2: Digital Silos
Digital silos or, “islands of automation,” use automation and digitized data, but systems aren’t connected to each other. These plants rely on local batch recipes and site-specific systems. Using analytics to discover why something happened takes time and manual effort.
Phase 3: Connected Plant
A connected plant is where a smart manufacturing platform with a digital quality management, employee resource planning (ERP), asset performance management (APM) and manufacturing execution system (MES) can shine. In a connected plant, automation systems are connected under one platform. Plant-wide analytics are centralized in one location and can be used for root cause analysis and automated documentation.
Phase 4: Predictive Plant
In phase four, your data starts to proactively work for you. Instead of just identifying why something happened, you can start to predict what will happen and when, so you can make better decisions to optimize processes and maximize value.
Phase 5: Adaptive Plant
The final phase means closing the loop automatically and using data across the entire enterprise. In this scenario, AI and machine learning can use data to continuously learn, re-train and adjust. The result is a “self-aware,” autonomous, adaptive plant that can self-optimize with minimal manual input.
WHAT ARE THE RESULTS OF IMPLEMENTING SMART MANUFACTURING SOLUTIONS?
Once you’ve assessed where you are on your digital transformation journey, how do you progress to the next phase? Rather than deploying isolated point solutions, companies should focus on building a digital-ready infrastructure that simplifies, cybersecurity, patch management and data contextualization.
Think of digital-ready infrastructure like adding apps to a smartphone. Once your foundation is in place, so you can start adding technology and services to accomplish goals like these:
Empowering Workers
With a skilled labor shortage and high turnover, upskilling workers and automating processes is critical. Giving workers tools like mobile devices with access to MES information and augmented reality applications can help workers learn processes faster and reduce your investment in training.
Autonomous mobile robots and industrial robotics can reduce material handling and allow you to re-deploy workers for more fulfilling, value-added tasks.
Optimizing Production and Asset Management
In addition to optimizing your workforce, smart manufacturing solutions can optimize your production. Smart machine technologies like independent cart technology and Unified Robot Control can reduce changeover time by 50% and simplify programming, while software solutions like FactoryTalk Batch and Fiix can help manufacturers reduce process variability and reduce maintenance costs.
Managing Risk
While cybersecurity might be the most obvious risk you can address with smart manufacturing, risk management includes product traceability, quality control, regulatory compliance, supply chain management and more. Digitizing quality data with a QMS automates regulatory compliance while empowering manufacturers to trace materials and quickly resolve quality issues.
For cybersecurity, continuous threat detection allows manufacturers to respond quickly to cyber threats and protect their intellectual property.
Driving Sustainability and Energy Management
Sustainability is a growing priority, but why? Over half of manufacturers (55%) say improving efficiency is the top reason to pursue better sustainability.3 Smart manufacturing tools help monitor and optimize energy use, automate compliance reporting and even schedule production based on energy demand. This not only reduces costs but also supports environmental goals.
TAKE YOUR NEXT STEPS IN SMART MANUFACTURING
Are you ready to start implementing smart manufacturing solutions? Here’s a road map to get you started:
- Start with a clear problem, not just a solution you want to try.
- Get a W! Prioritize projects based on impact and ease of implementation.
- Engage your workforce. Their buy-in is critical.
- Celebrate and scale your successes to maintain momentum.
Looking for more personalized next steps you can take?
Let us know which statement best describes the current state of your digital strategy, and we will follow with specific solutions tailored to your needs.
References:
About the Authors:
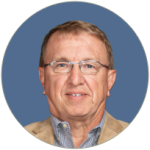
JERRY PLESSING
Global Industry Consultant, Rockwell Automation
Jerry Plessing has been advising leaders in manufacturing looking to transform their organization for 40+ years. He is currently global industry consultant with Rockwell Automation where he is responsible for guiding customers through their Smart Manufacturing journey, focusing on the necessary products/technologies to ensure a successful deployment. He currently is based out of Omaha, Nebraska and supports RA's global CPG customer base. Jerry holds both a Bachelor of Science and a Masters in Agricultural Engineering from University of Nebraska-Lincoln.
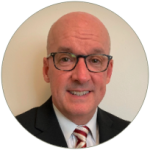
TODD GILLIAM
Americas Industry Leader, CPG, Rockwell Automation
Todd Gilliam leads strategic initiatives to drive growth in the company’s largest industry vertical. He works closely with manufacturers to address evolving business challenges and guides them through their Digital Transformation and Connected Enterprise journeys. With over 35 years of experience in manufacturing software, industrial automation, and consulting services, Todd brings a wealth of industry knowledge to his role. Prior to joining Rockwell Automation, he held leadership positions at Microsoft, Oracle, and ABB, where he helped shape digital strategies for global manufacturing clients. Todd holds a Bachelor’s Degree in Electrical and Computer Engineering from the University of South Carolina.